Overlooked challenges in digital twin
Digital twins offer companies in heavy industries like oil and gas and mining incredible opportunities to increase safety, optimise resources, and reduce downtime. However, none of this is possible without the unsexy, underlying work that is required. One of the greatest (and most underestimated) digital twin challenges is what it takes to keep them operating sustainably.
Digital twins need fresh, relevant, useful data. Without it, digital twins become mere snapshots of the point in time where they were created, without any of the benefits an engineering digital twin are meant to offer.
Despite this, data maintenance is one of the first things to fall through the cracks – especially when a digital twin is handed over to operations from the EPC (Engineering Procurement and Construction). Here are some of the main factors that owner operators should consider when looking after a digital twin.
Not just a 3D design update
A lot of errors start from a misunderstanding of digital twin tech. You’ll often see engineering digital twins represented as a dynamic, 3D visual representation of a physical asset. While data visualisation is certainly one of the many benefits of digital twin tech, it isn’t the core of how digital twins work.
Updating and upgrading your 3D model shouldn’t be your only priority in operating digital twins. Instead, the most useful aspect of a digital twin is the updatability, quality and relevance of its data. Essential systems like feedback loops allow a digital twin to evolve with its physical counterpart. But if data feedback loops aren’t working, the accuracy of your digital twin’s modelling will be greatly compromised.
Decide who's in charge
A main cause of poor data maintenance is lack of clarity in duties and responsibilities. You need a team whose job it is to keep all the information fed into your digital twin current, complete, and correct.
Decide who’s going to maintain the data after handover to operations, and make sure they commit to it. Define clear roles, automation tools, and data governance protocols. Implement everything into your team’s normal workflows.
Why do we need data governance?
Implementing clear data governance practices ensures that the data fed into the digital twin remains reliable, stable, and secure. This is especially important when you handle huge siloes of data. By setting parameters for frequent updates, and defining data sources and attributes, your team can function effectively and consistently – and avoid slipups.
Keep an eye on cross-integration
Digital twins don’t rely on just one stream of data, and they certainly don’t exist in isolation. Good digital twin implementation requires interoperability and cross-integration of data.
Consistent interfacing with key systems like SAP, intelligent P&ID, and 3D modelling ensures greater integrity. The systems you use matter, especially when they integrate with ERP and CMMS for data flow and management.
It might also help to have a physical strategy for data maintenance. For example, can engineers and technicians easily input real time data into their phones or devices while they’re working in the field?
The demands of interoperability in digital twins for owner operators will change over time, and you’ll have to adapt accordingly. It’s essential that you continuously monitor and improve the mechanisms you use to receive, manage, and process data.
Don't eat the cost of digital twin challenges
The cost of not maintaining your digital twin’s data and ensuring proper data governance can be high for oil and gas companies. Data maintenance isn’t glamorous work, but it’s necessary.
Whether you’re in the oil and gas sector, or are involved in mining and chemicals, there’s a reason why you operate within strict maintenance schedules and safety standards. Inaccurate data can mislead engineers, technicians, and other members of your team, resulting in costly errors. At best, your experience unnecessary shutdowns and inefficiencies, and at worst, you risk the safety of everyone working in your plants and factories.
Finding the right solution can help you make the most out of your digital twin solution, and avoid increased risks. If you’re not sure how to overcome digital twin challenges, the Draga team is ready to help. We’re not just experts in digital transformation – 70% of our team are engineers with years of working in oil and gas. Contact us today.
You May Also Like
These Related Stories
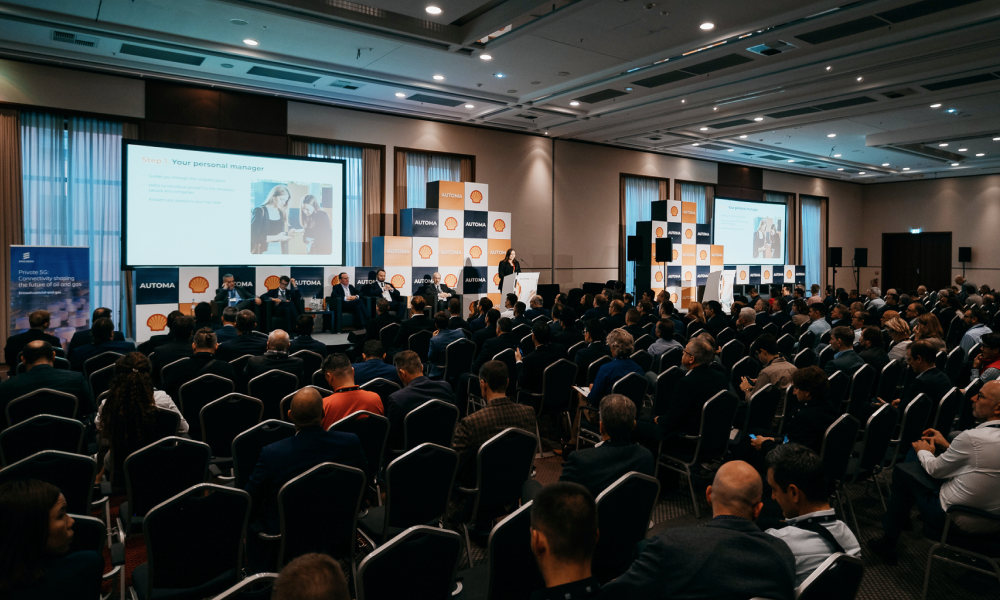
An optimistic future for decarbonisation in oil and gas
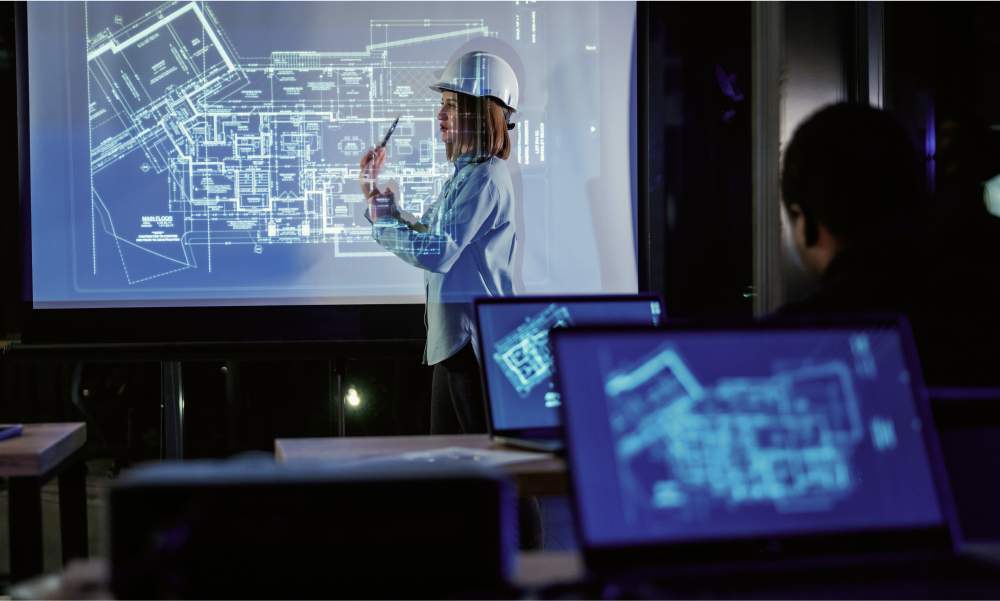
The role of data management in building a digital twin
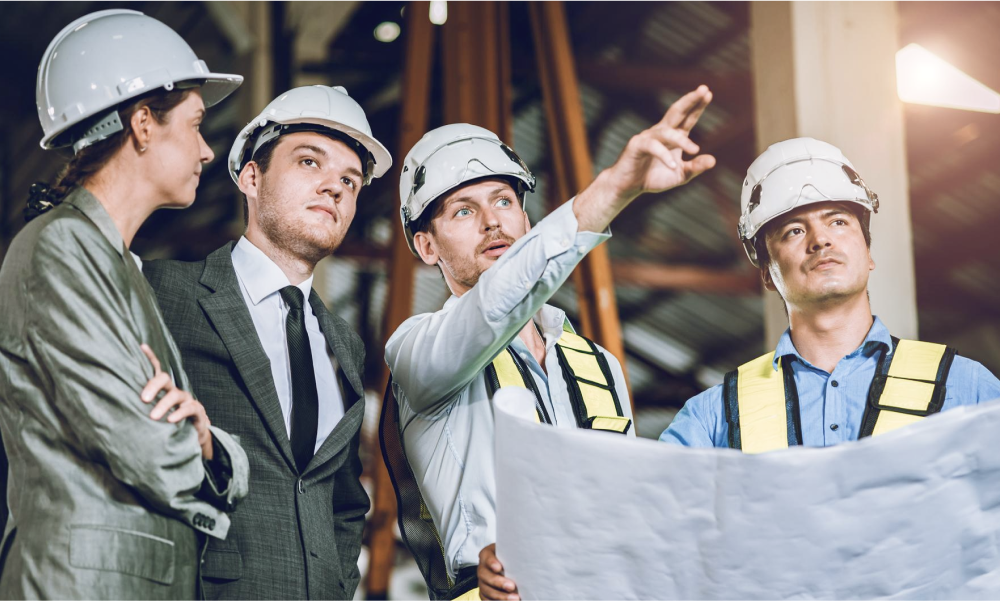