Why is engineering digital twin technology important?
What is digital twin technology and how does it benefit engineers and key decision-makers? A digital twin is a virtual representation designed to reflect a physical object, person, or process with the context of its environment, using real-time data. Integrating and engineering digital twin technology has several uses and advantages in every industry.
Digital twins can be used to replicate a wide variety of things, including:
- Products throughout their entire life cycle
- Manufacturing plants or processes
- Physical infrastructure
- Supply chains and transportation
- Computer and data networks
- And much more!
A quick history of digital twin engineering
The concept of ‘digital twins’ was originally introduced by Dr. Michael Grieves at the Society of Manufacturing Engineers conference in 2002. However, one of the earliest digital twin examples is NASA’s careful engineering used to study and simulate the very first landing. (NASA remains one of the pioneers in digital twin technology today.)
More than static models and simulations
Digital twins draw from simulations, IoT (Internet of Things) networks, and machine learning technologies to create a replica in virtual reality. However, digital twins are more than computer-aided models. They are dynamic entities that evolve and communicate with their real-life counterparts. Huge amounts of data is collected in real-time, processed by a set of analytics or algorithms, and is used in executive controls to optimise operations.
Real-time data also means that the digital twin and its real-life counterpart mirror each other as closely as possible. Whether represented in a 3D model or in other forms of simplified, organised data, digital twins are incredibly useful tools for managing assets and resources.
Digital twin engineering provides key insights into how an asset or process might interact with its environment, by simulating real-world conditions. Engineering digital twin technology is used to manage maintenance, support decommission, and strategize future use.
Types of digital twins
- Component twins: As the smallest form of digital twin, these are used to replicate a single part of an entire system, for example a motor in a wind turbine.
- Asset twins: When two or more components work together, they form an asset. In engineering digital twin assets help to understand how components work together.
- System twins: These help you see how different assets come together to form a functioning system. Insights from these digital twins help you understand how to enhance performance and eliminate inefficiencies.
- Process twins: These digital twins help understand how systems work together to create a production facility.
Driven by data collection and digitization
The key connecting thread between an asset, process or system and its digital twin is data.
The type of data that is collected and used depends largely on the purpose of the digital twin, the physical object or process being replicated, and when the digital twin is constructed.
So, for example, in a new build, a digital twin is created at the outset of a project and continually mapped with operational data. Or, if a company is investing in a digital twin for pre-existing processes or assets, you can create a digital twin by installing a comprehensive IoT network, sensors, and drawing from existing data silos. It can be an intensive investment, however the benefits lead to significant ROI.
The frequency and fidelity of the data collected can vary, depending on how up-to-date and accurate the digital twin needs to be. You might need thousands of sensors for a particularly complex piece of machinery in extreme weather conditions.
What is absolutely necessary is digital maturity of the company or organisation adopting digital twin technology. In order to create and operate a digital twin, there already needs to be in place high-quality data infrastructure that delivers reliable data from testing and live environments. You’ll need the storage and processing capabilities that will allow your teams to access the digital twin from anywhere. This usually requires digital transformation and an overhaul in how you work together as a global organisation.
The benefits of digital twin technology
There are several benefits to engineering digital twin technology. Engineers can monitor, manage and construct physically large objects or mechanically complex projects.
Digital twins also unlock data trapped in silos or paper files. From design to decommission, more members of your team can access information that’s orderly and easily accessible, while integrating static and dynamic data. For example, maintenance schedules can be compared to actual wear and tear and environmental conditions, allowing your engineers to take action at the first sight of trouble rather than waiting for things to break down.
With digital twins, engineers and decision-makers can build a digital thread for better traceability, and refine assumptions with predictive analytics. Engineers are able to test new processes and protocols for maximum effectiveness and safety. You can mirror and monitor processes, logistics and machinery from anywhere in the world – allowing for more remote or offshore work.
How can digital twins help the oil and gas industry?
Digital twins have been implemented in a range of industries, from aviation to city planning. This technology also plays a key role in the digital transformation of the oil and gas sector. Some key digital twin use cases in oil and gas include:
- Designing better offshore drilling platforms. Digital twins help better manage the huge financial and safety risks associated with tapping new reservoirs by utilising geodata. Reservoir simulations can also help avoid environmental problems and avoid losing hundreds of millions of dollars.
- Empowering offshore engineering by removing several requirements for engineers to be at your location physically. Digital twins can even offer more insights and context than would normally be available onsite.
- Identifying asset lifespan by analysing stress and fatigue levels, structural problems, and anomalies.
- Improving midstream processes by identifying congestion points and optimal routes. Teams can simulate and test logistics that save precious time, while improving distribution chain efficiency.
- Optimising downstream products. Digital twins can identify bottlenecks in production lines, processes, and systems.
- Planning through business and market forecasting. Digital twins can monitor and predict changes in oil and gas supply, price fluctuations, and global events.
- Increasing safety and recreating emergency scenarios like fires or spills in a virtual environment.
Ultimately, taking the leap to engineering digital twin technologies leads to greater ROI for owners, smoother operations, and more transparency. If you’re interested in learning how digital solutions can benefit your business, get in touch with us today for an informal chat.
You May Also Like
These Related Stories
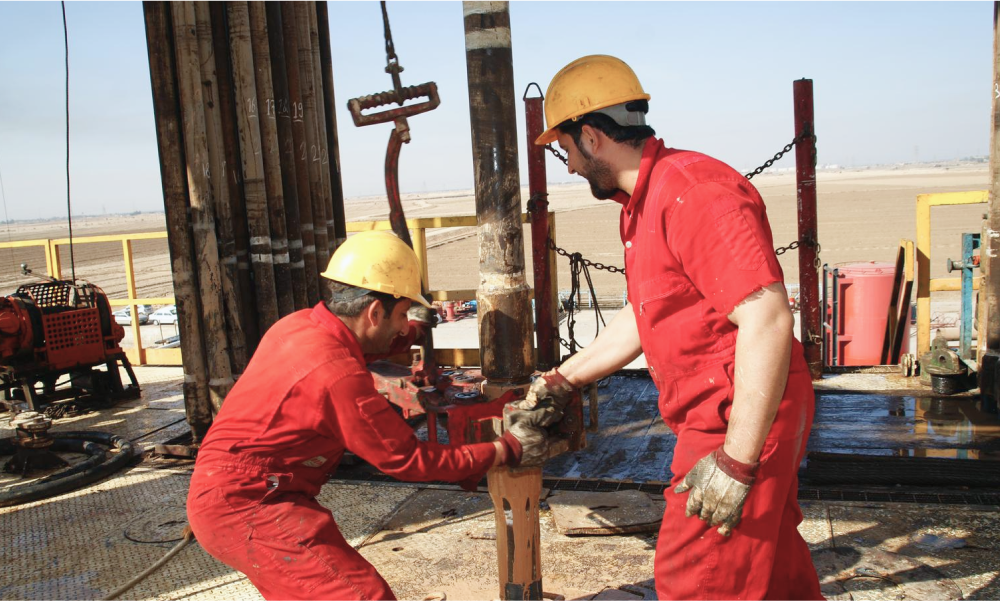
Can digital twins drive decarbonisation?
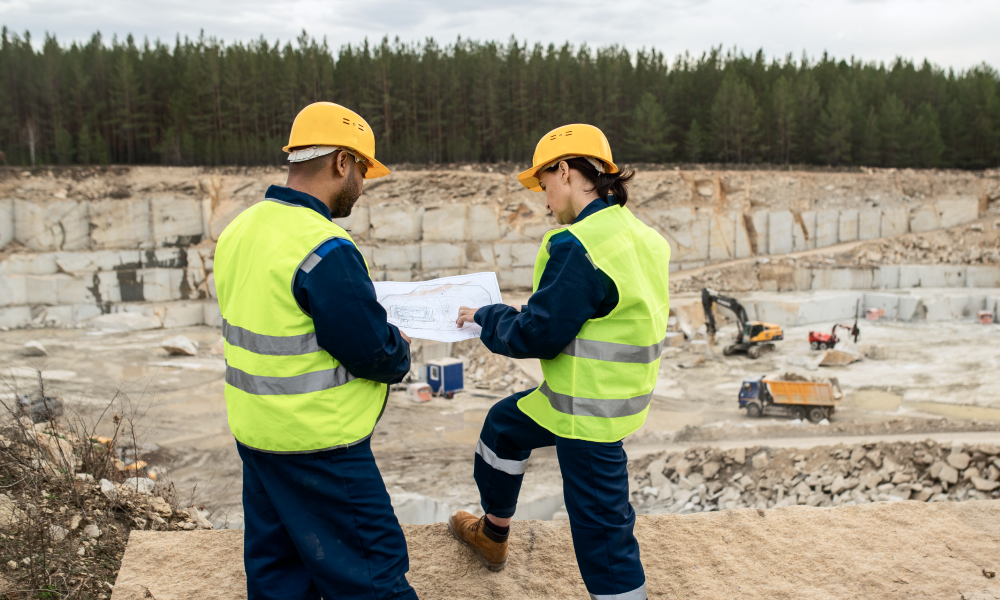
Overlooked challenges in digital twin
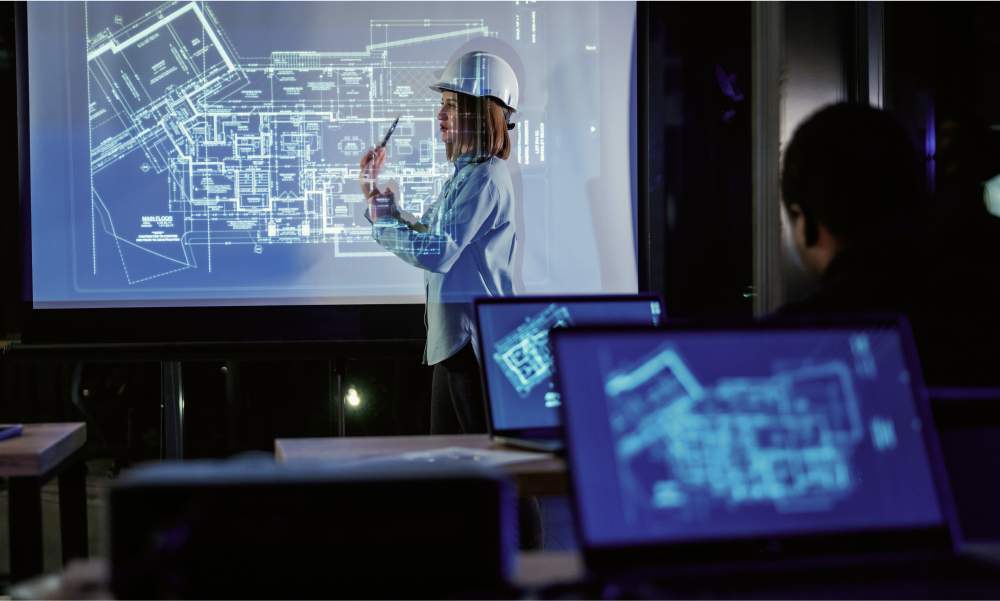